Our Guide to Semi Truck Repair and Preventative Maintenance
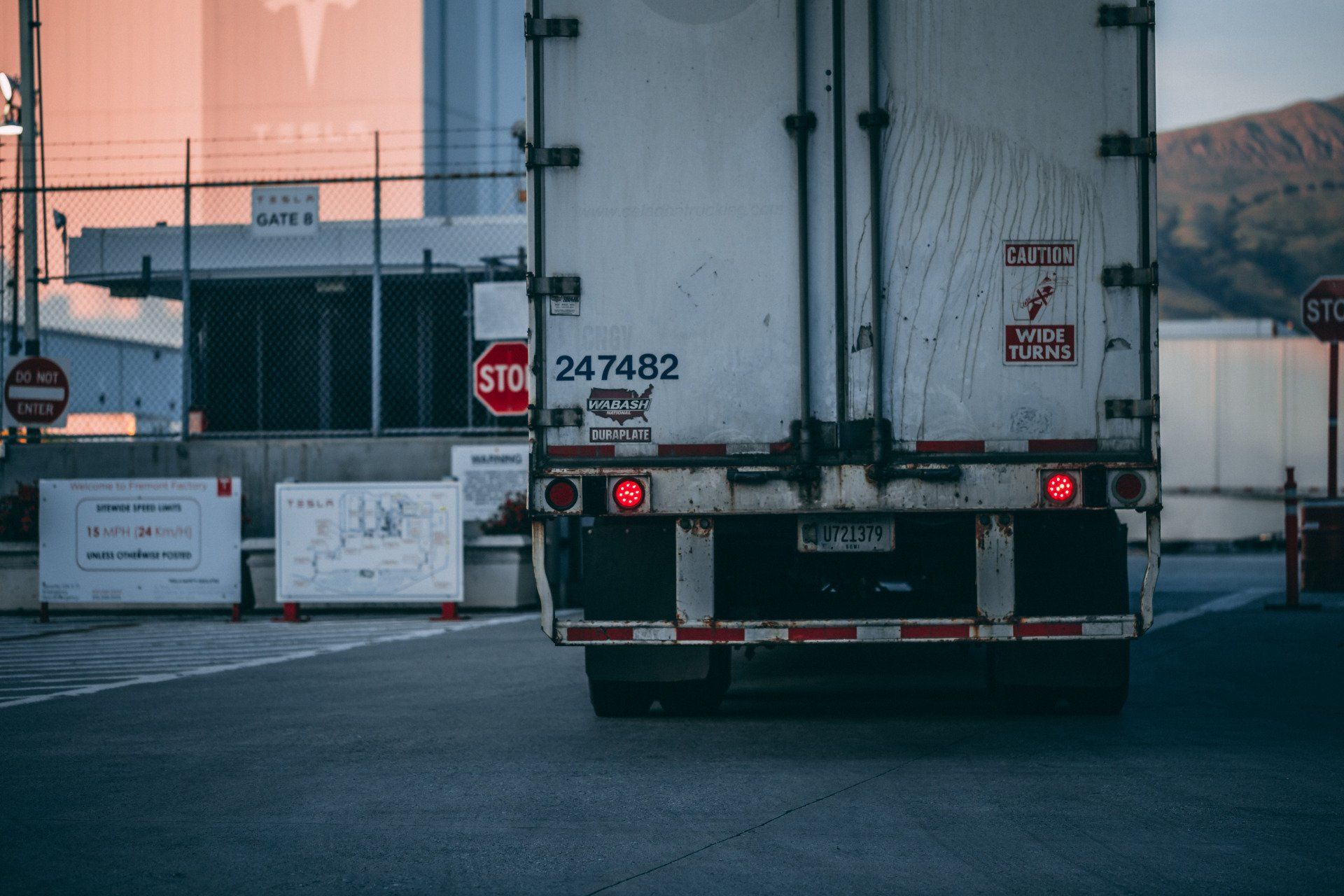
Keeping your fleet of semi trucks up and running is critical to the success of your transportation or logistics business. When trucks break down or need maintenance, it leads to expensive repairs and lost revenue from being out of service. Performing regular maintenance and understanding when to take trucks in for servicing is key to maximizing uptime.
Here are some expert tips and strategies for keeping your semi trucks in good working order. Follow these semi truck repair tips and you'll keep your trucks rolling down the highway.
The Most Common Semi Truck Maintenance Issues
Semi trucks are complex machines with many parts that need regular inspection and maintenance. Some of the most common issues that crop up include brake problems like worn brake pads, damaged rotors, brake fluid leaks, and other brake issues that can compromise safety.
Electrical system issues such as corroded wiring, bad alternators, and faulty lighting can cause starting problems or complete breakdowns.
Tire wear and punctures are also common, as worn treads make blowouts more likely and nails, road debris, and potholes can cause punctures.
Leaking or damaged hoses that are cracked and dry-rotted need to be replaced before catastrophic failure. Fluid leaks in engines, differentials, and hydraulic systems need prompt attention to avoid breakdowns.
Suspension and alignment problems arise as shocks and struts wear out over time and misalignment causes uneven tire wear.
Regular inspections and preventative maintenance will spot most of these problems early before they strand a truck on the side of the road. Timely repairs prevent bigger breakdowns.
How to Tell if Your Semi Truck Needs Repair: Signs to Watch For
Experienced drivers will notice small changes in how their truck handles or sounds that indicate a deeper problem. But there are some clear signs that inspectors and drivers should watch for. These include strange new noises from the engine, brakes, axles or wheels, such as knocking, squealing, or grinding that signal component wear. Smoke from the exhaust, especially white or blue smoke, indicates burning oil or antifreeze.
Dashboard warning lights related to the engine, battery, or other systems point to issues, as do diagnostic trouble codes. Leaking fluid visible on the ground under the truck in pools of oil, coolant, brake fluid, or other liquids is a concern. Vibrations felt in the steering wheel, seat, or floorboards at certain speeds point to unbalanced wheels/tires or driveline issues. Pulling to one side when braking indicates potential brake problems or seizure in a wheel hub.
High engine temperature readings, steam from the hood, or overheating signals problems with the coolant system. When drivers notice any of these warning signs, it's smart to pull over and call for service rather than continuing down the highway, as timely repairs prevent bigger breakdowns.
The Critical Importance of Regular Maintenance for Semi Trucks
The backbone of any good maintenance program is performing thorough inspections and routine servicing at regular intervals. Follow the manufacturer’s recommendations for oil changes, filter replacements, lubrication, and other basic maintenance. Don’t overlook scheduled servicing items like changing air, fuel, and oil filters, draining water separators, checking U-joints, adjusting brakes, flushing coolant systems, replacing hoses and belts, wheel bearing repacks, and full brake overhauls.
Repairs can be expensive, but diligent maintenance is relatively cheap and will significantly extend the useful life of all major components. Proper preventative maintenance catches issues before they become major.
Minor Repairs DIY Tips
Some basic repairs like light bulb or fuse replacements, minor oil leaks, worn wiper blades, or loose mounts can be performed by the driver or technician in the field. This gets the truck rolling again quickly. When tackling minor repairs, be sure to follow OEM procedures in service manuals, use quality replacement parts that meet specifications, and have proper tools for the job. Know your limits - don’t attempt complex repairs roadside. And document all repairs and parts replacements. Quick roadside repairs keep small issues from becoming headaches down the road.
How to Choose the Right Repair Shop
For major engine or transmission overhauls, collision repairs, warranty work, and complicated electrical issues, rely on a professional shop with trained technicians and the right tools. Look for shops with a solid reputation for quality work and customer service. They should have specific experience working on heavy trucks with technicians specializing in areas like brakes, electrical, or drivetrain. State-of-the-art diagnostic scanners and repair information systems are a must. Choose a shop that can complete repairs quickly to minimize downtime, provides warranties on parts and labor, offers preventative maintenance packages, and shop that you can trust to do the job right. An incompetent shop can cause as many problems as they fix, so do your research.
Preventative Maintenance Tips
The key to avoiding surprise roadside breakdowns is diligent preventative maintenance. Stick to scheduled maintenance intervals per OEM guidelines. Don’t cut corners. Perform thorough pre-trip and post-trip inspections, as your drivers are the first line of defense. Confirm all previous repairs were completed properly. Watch for recurring failures and schedule proactive repairs when issues persist.
Keep detailed maintenance records on each vehicle. Listen and respond quickly to driver concerns. Fix small problems before they snowball into major repairs. Replace worn parts before they fail. Use high-quality fluids and parts. Perform basic servicing like cleaning radiators, load testing batteries, lubricating hinges, inspecting tires, and so on. Preventative maintenance takes commitment and discipline but avoids catastrophic failures at the worst possible times.
How to Budget for Repair Costs
It’s impossible to predict exactly when trucks will need repairs. But you can forecast average repair and maintenance costs over the lifetime of your vehicles. Review past repairs to estimate costs of major components. Research typical costs for common repairs. Factor in rising parts and labor costs over time. Account for regular preventative maintenance like oil changes. And build in a contingency fund for unexpected failures.
With an estimated budget, divide total projected costs by the miles you expect to accumulate. This gives a good cost per mile for repairs and maintenance to compare against operating costs per mile. This helps make management decisions that optimize your fleet.
Tips for Keeping Your Fleet on the Road
Your goal is maximum uptime and minimum unscheduled maintenance. Hire qualified, safety-focused drivers, and provide ongoing training to keep skills sharp. Implement policies against neglecting maintenance or abusing equipment. Provide incentives for drivers who practice safe habits and meet maintenance goals. Install GPS fleet tracking to monitor driving habits that increase wear.
Don’t overload trucks beyond axle limits. Replace trucks at the optimal time before age leads to excessive maintenance. Store spare parts to complete repairs quickly if needed. And have contingency plans for breakdowns or substitute trucks. Keep your fleet well maintained and train your team for maximum productivity.
Fleet Management Software
Sophisticated software can track all aspects of fleet maintenance. It records repairs and scheduled maintenance on each vehicle, provides automated reminders for preventative maintenance, manages driver vehicle inspection checklists, controls parts inventory and ordering, tracks warranties, wirelessly uploads diagnostic codes, and generates custom reports and analytics. Software gives visibility into metrics so you can make data-driven decisions that optimize fleet uptime.
Detailed Maintenance Schedules
For each vehicle, implement a complete preventative maintenance schedule that covers recommended servicing intervals per OEM guidelines. Include standard items like oil changes, major component servicing like transmission flushes, compliance items like emissions maintenance, tire rotations, annual inspections, and so on. Tracking schedules for individual trucks ensures critical services aren't missed, and software makes this easier.
Choose Quality Parts
Don't compromise long-term reliability and durability to save money upfront. Use OEM or OEM-quality replacement parts, premium oils/lubricants/filters, top brands known for truck reliability, and components with manufacturer warranties. Pay a little more for quality parts that meet original engineering specs and stand the test of time. Cheap knock-offs often fail prematurely.
Keep Accurate Records
Document all repairs and maintenance performed on each vehicle, including the date/mileage, driver who reported the issue, detailed description of the problem, diagnostic findings, parts replaced, labor hours, and name of the shop doing the work. Complete maintenance records help spot recurring issues early, predict future repair costs, and provide critical documentation if needed for warranty or legal claims.
Perform Regular Inspections
Don’t rely solely on driver reports to detect maintenance needs. Perform recurring hands-on inspections, including annual or semi-annual bumper-to-bumper inspections by a qualified mechanic. Do a monthly walk-around checking tires, lights, fluid levels, etc. And ensure quick pre-trip and post-trip driver inspections before and after each haul. Inspections reveal concerns like leaks, loose parts, tire wear, squeaks, and other issues drivers may miss. Address them before trucks break down.
Contact Mainline RV & Truck Service for Semi Truck Repair
Don’t let maintenance disrupt deliveries and revenue. The experts at Mainline RV & Truck Service can handle any semi truck repair quickly and correctly. Contact our team today to learn more about our semi truck repair and maintenance services.
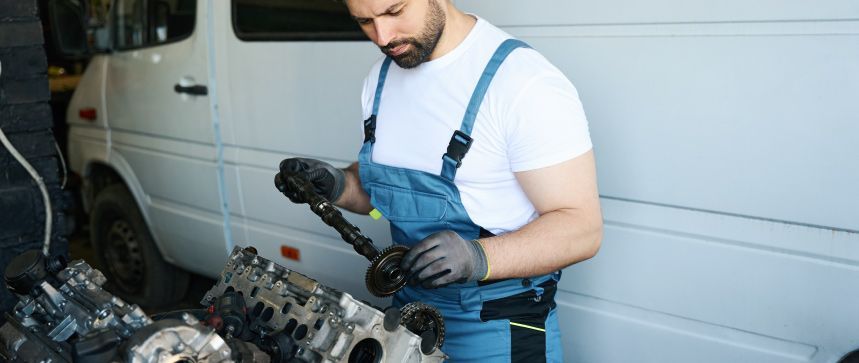
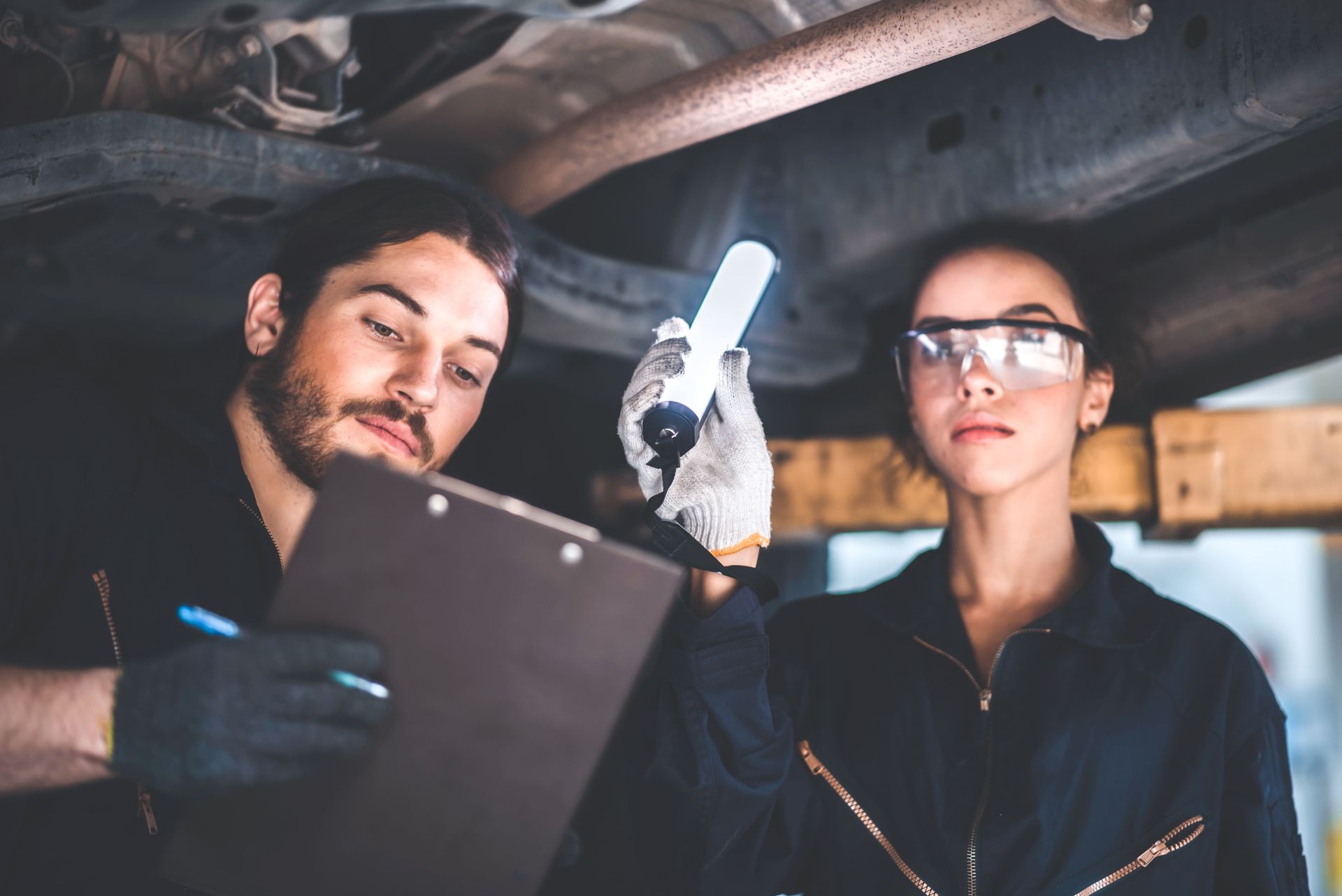