Five Simple Ways to Avoid Fleet Downtime
Keeping downtime to a minimum is essential in the trucking business. Downtime often makes it impossible to meet delivery deadlines, which always results in unhappy customers. Looking at all of the different ways to reduce downtime in the shipping industry is important in helping you build your reputation while creating a much less stressful environment.
Here are a few simple ways you can avoid fleet downtime.
1. Preventative Maintenance
Scheduling preventative maintenance is key to success in the trucking industry. Reaching out to a truck service company can often help you identify any potential issues before they become more severe and leave your drivers stranded on the road. A truck service technician can perform a variety of tasks, such as checking the air in the tires, replacing dirty air filters, and other adjustments.
2. Schedule Repairs
Dealing with repairs is a common issue for trucks. Contacting a local truck repair shop is a great way to take care of these issues as soon as possible before they get worse over time. These professionals can handle all types of truck repairs to help your drivers get back on the road as soon as possible.
3. Always Listen to Your Drivers
Staying in communication with your drivers is key in identifying any potential problems with your trucks. Always asking for feedback will help you understand if you need to get a truck inspected for any problems ahead of time before it's too late.
4. Install Speed Limiters
Speeding increases the risk of accidents, and it also causes excess fuel consumption. Installing a speed-limiting device on each truck is a great way to avoid these issues. You can also reduce wear and tear on each truck, which helps to limit downtime.
5. Build a Relationship with a Truck Repair Company
Not all truck service and repair companies are equal. Checking out online reviews and asking for any recommendations can help you find the best repair shop in your area. Building a strong relationship with these professionals will help you limit downtime and keep your trucks running at an optimal level.
Effective Strategies for Avoiding Fleet Downtime
Fleet downtime is a challenge that trucking companies face when vehicles in their fleet are out of service due to maintenance issues or unexpected breakdowns. As fleets continue to grow and vehicles age, minimizing fleet downtime has become a critical task for fleet managers to ensure smooth operations, and to maintain profitability. Here are some strategies to avoid fleet downtime, maintaining optimum productivity with downtime fleet management services.
The Risks of Truck Fleet Downtime
Lower Productivity
Downtime directly affects the productivity of a fleet. When a vehicle is out of service, it means there's a decrease in the number of loads a fleet can move in a day. This lower productivity can impact customer relationships and brand reputation.
Costs of Repairs
Frequent downtime results in increased maintenance and repair costs. These expenses can quickly add up, especially if you're dealing with older vehicles that require regular, extensive repairs.
Revenue Loss
Each hour that a truck spends in the shop rather than on the road translates to a significant revenue loss. This, combined with the repair costs, can severely impact the profitability of a fleet operation.
Replace Older Vehicles in the Fleet
As a fleet manager, it's important to assess the life-cycle cost of your vehicles. Older vehicles might seem cheaper in the short term, but they often require more maintenance and are prone to unexpected breakdowns, leading to increased downtime. Regularly replacing older vehicles in the fleet with newer, more reliable ones can significantly decrease downtime.
Regular Inspection and Repair
Preventive maintenance is one of the most effective ways to avoid fleet downtime. Regular inspections and timely repairs can help identify potential issues before they cause serious problems. By catching these problems early, you can address them before they lead to significant downtime.
Always Encourage Safe and Conservative Driving
Driver behavior plays a significant role in the health of your fleet. Encouraging safe and conservative driving can reduce the risk of accidents and wear and tear on your vehicles, thus lowering the frequency of repairs and downtime.
Getting the Right Trucks
Getting the right trucks for your fleet involves analyzing your business needs and choosing vehicles that suit those needs. For instance, if your truck is often drive on rugged terrain, investing in vehicles designed to withstand such conditions will reduce the chances of breakdowns and downtime.
Don't Delay Maintenance
Delaying maintenance can lead to bigger problems down the line. It's crucial to keep up with all scheduled maintenance, including oil changes, tire rotations, and brake inspections. By keeping on top of these tasks, you can prevent small issues from escalating into major problems that can cause extended downtime.
Make the Most Out of Any Downtime Event
Despite your best efforts, downtime events are sometimes inevitable. You should make the most of these events by utilizing this time to complete any pending maintenance tasks, train drivers, or update software systems.
Expect Fleet Downtime
Always have a plan in place for when downtime occurs. This might include strategies for rerouting deliveries, managing client expectations, and speeding up repair times. Being prepared can help mitigate the impact of downtime on your operations.
Have Backup Vehicles Ready
Depending on the size of your fleet, having backup vehicles ready to step in when primary trucks go down is a useful strategy for managing downtime. This means you can continue operations while repairs are happening, thereby avoiding a complete halt of services.
Service Reminders
Use fleet management software to send service reminders and alerts. This can help ensure regular maintenance tasks aren't overlooked and can keep your fleet running efficiently.
Vehicle Timelines/Lifespans
Understanding the lifespan of your vehicles can help you plan for replacements and avoid unexpected downtime. Regularly track the performance and maintenance records of each vehicle in your fleet to better estimate their lifespan and schedule replacements.
Track Repair Data from the Shop
Tracking data from the shop can provide valuable insights into common issues your fleet is facing. You can use this data to identify trends, predict future breakdowns, and devise preventative strategies.
Contact Mainline RV & Truck Service for Reduced Downtime Fleet Management
Mainline RV & Truck Service offers repair and maintenance for a variety of customers. We have over 35 years of experience in the industry, as we pride ourselves on always providing top-quality truck repair services. Give Mainline Truck & Trailer Service a phone call today to learn more!
When dealing with fleet downtime, you need to have experts on your side. Contact Mainline RV & Truck Service for professional downtime fleet management. We offer comprehensive solutions designed to reduce fleet downtime, enhance efficiency, and support your bottom line.
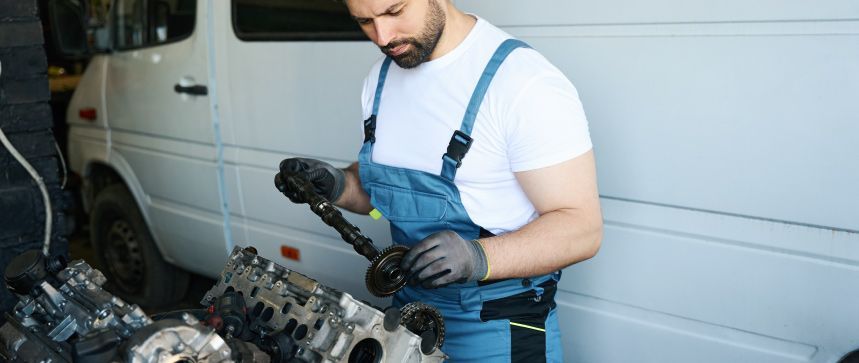
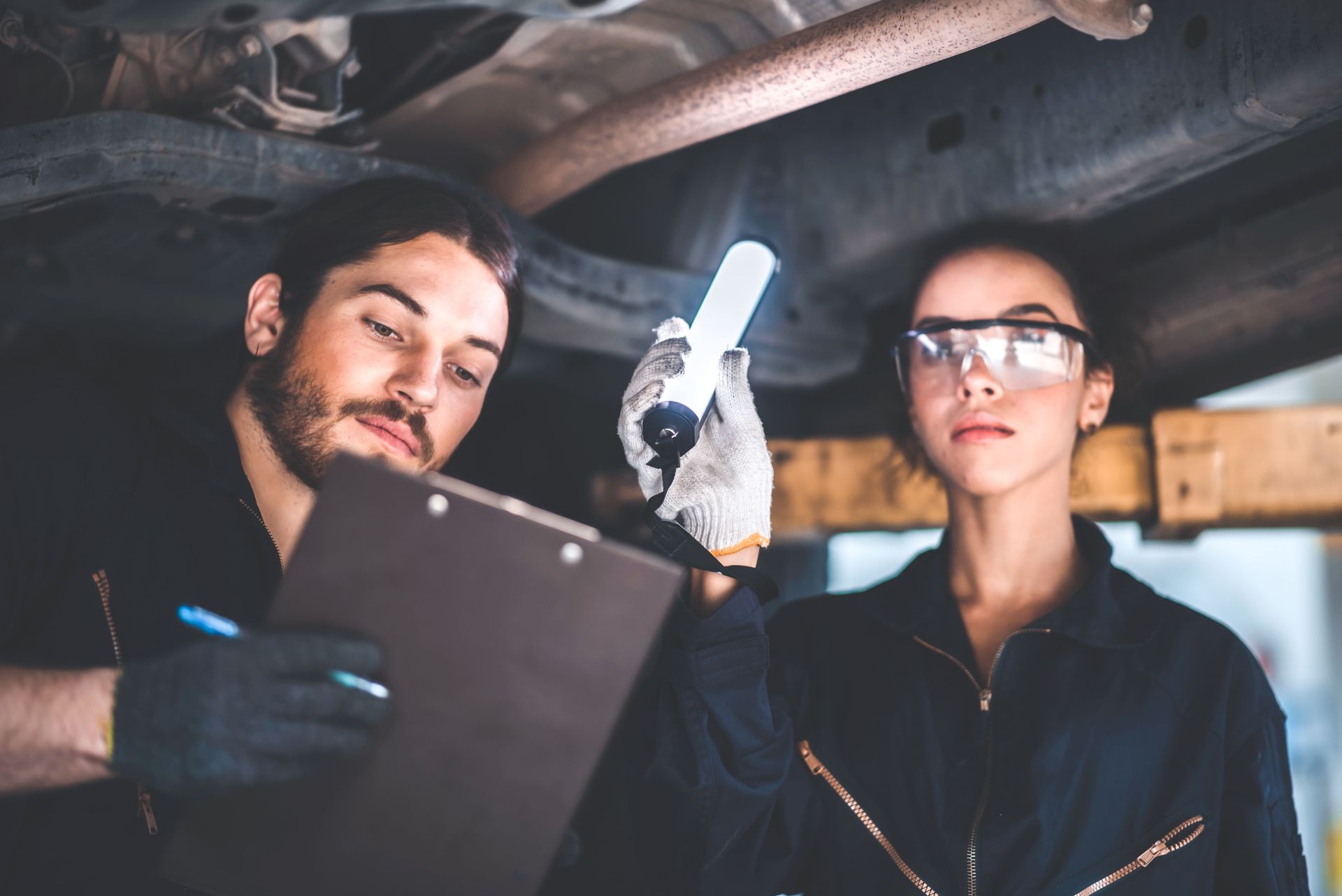